- completed
[TPF]
Interfacial Behaviors and Heat Transfer Characteristics in Boiling Two-Phase Flow
- Physical Science
ISS Science for Everyone
SCIENCE OBJECTIVES FOR EVERYONE
The JAXA Interfacial behaviors and Heat transfer characteristics in Boiling Two-Phase Flow (Two-Phase Flow) experiment investigates the heat transfer characteristics of flow boiling in the microgravity environment. This experiment provides a fundamental understanding of the behaviors of bubble formation, liquid-vapor flow in a tube, and how heat transfers in cooling systems. Two-phase flow employs a sample cooling loop using perfluorohexane, often used in coolant for electronics, to establish flow rate, heating power, and other effects on different conditions.
Experiment Description
RESEARCH OVERVIEW
- There is no cohesive database for the thermodynamics for the behavior of liquids in microgravity for boiling and two-phase flow. There is also a prevailing misconception that small differences exist between normal and microgravity heat transfer coefficients in boiling and two-phase flow, in the existence of bulk flow.
- The Interfacial behaviors and Heat transfer characteristics in Boiling Two-Phase Flow (Two-Phase Flow) investigation helps to provide better fundamental understanding on the behavior of liquid-vapor flow, and the mechanism of heat transfer under microgravity. This investigation also seeks to establish a database of thermodynamic data for microgravity boiling and two-phase flow. Finally, JAXA will establish a spacecraft standard for the thermal management system utilizing a boiling two-phase pumped loop.
- The knowledge obtained from Two-Phase Flow could be applied to the design of more efficient high-performance space thermal management systems for use in space applications.
Media Gallery
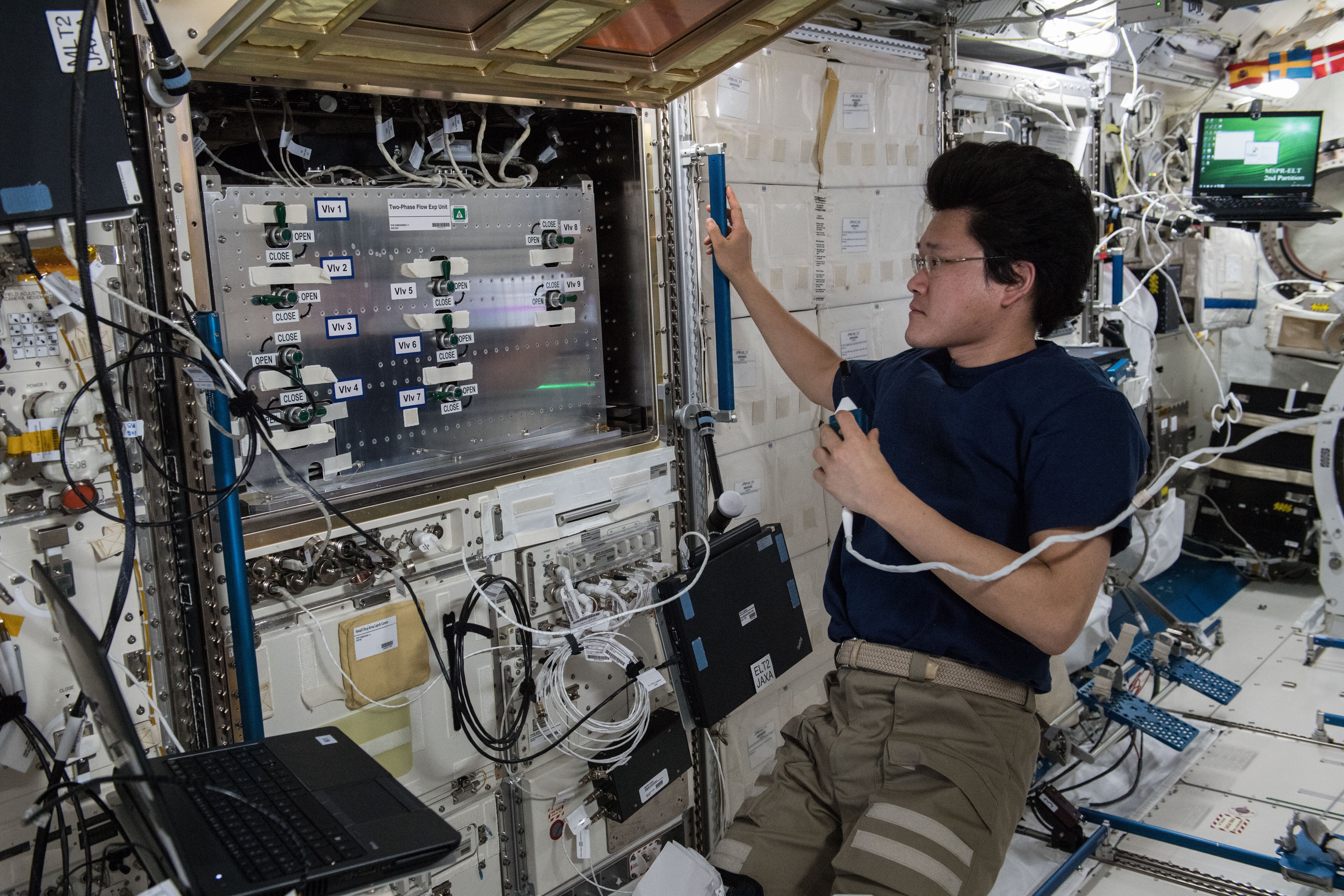
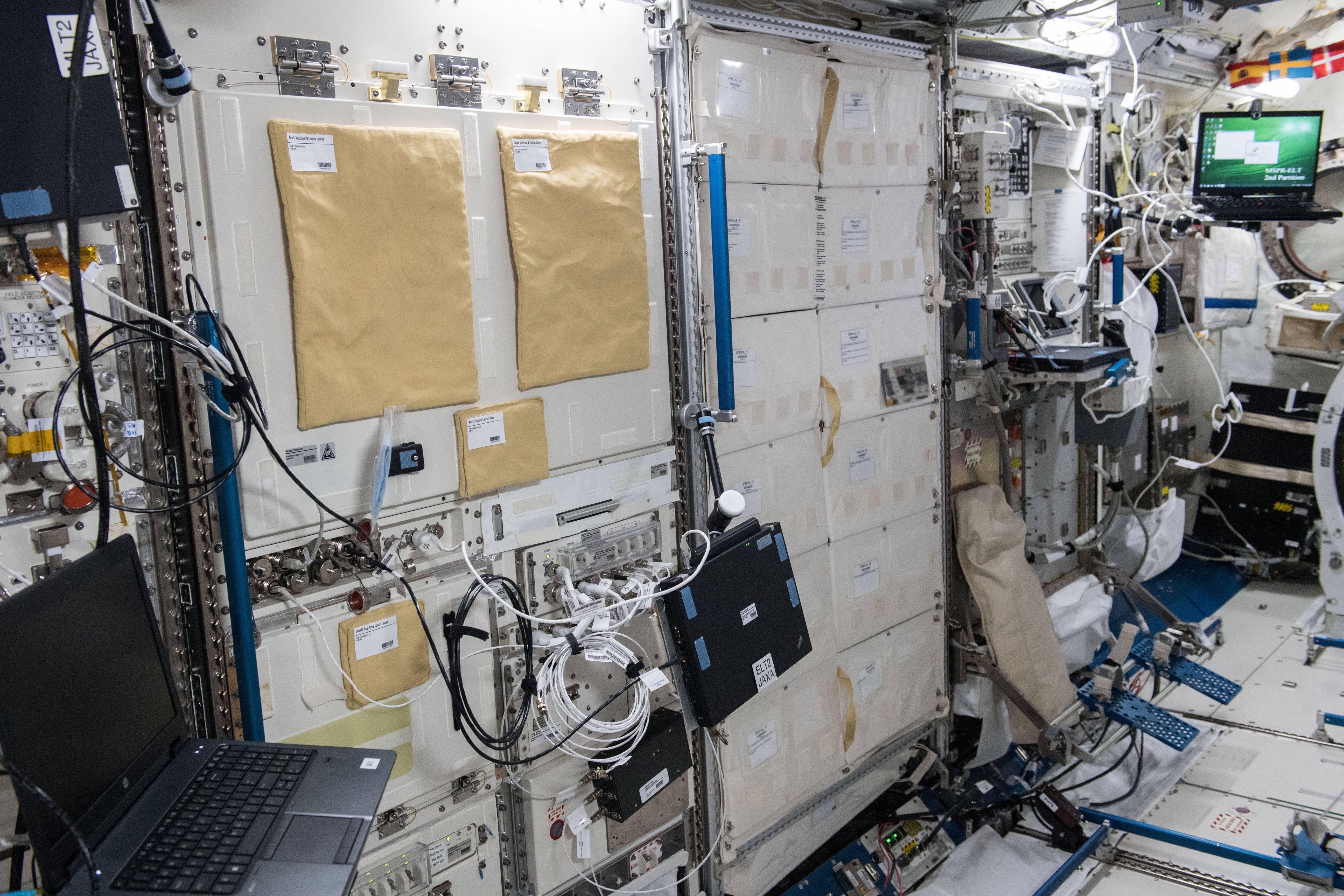
Applications
SPACE APPLICATIONS
Boiling normally removes heat by turning liquid into vapor at the heated surface, and that vapor returns to a liquid by way of a condenser which continues to cycle and make a cooling system. In the microgravity of space, the heat transfer rate must be changed because liquid and bubble behavior is drastically different than on Earth. This investigation seeks to build a database on the heat transfer efficiency of liquids in space that can be used in the design of high-performance thermal management systems for future space platforms.
EARTH APPLICATIONS
Results from Two-Phase Flow can also help to refine ground-based experiments on different cooling systems, since effects in microgravity often mimic what happens at smaller, faster scales on Earth. This investigation can support development of improved cooling systems for electrical power inverters in hybrid cars, and other electronics systems, where high heat levels are generated in small spaces and require large capacity cooling systems.
Operations
OPERATIONAL REQUIREMENTS AND PROTOCOLS
The Two-Phase Flow Experiment Equipment (TPF-EE) is installed in the JEM-Multipurpose Small Payload Rack Work Volume (MSPR WV). After the setup, staff operate the experiment from the ground as required by investigators at the Space Station Integration and Promotion Center, Tsukuba Space Center (SSIPC-TKSC).
The Two-Phase Flow experiment procedure is as follows:
1) before the experiment, TPF-EE is installed in the JEM-Multipurpose Small Payload Rack Work Volume (MSPR WV) by the International Space Station crew; 2) preparation of experiment [activation and initial setting of facilities (TPF-EE, MSPR, MSPR Experiment Laptop Terminal (ELT), Acceleration Sensor Unit (ASU)]; 3) experiment operation (circulating sample fluid (n-perfluorohexane) in TPF-EE test loop, applying heat flux to sample fluid, data correcting and video recording); 4) post experiment operation (playback downlink of recorded video images, downlink of test data measured by TPF-EE and acceleration data measured by ASU); and 5) closeout of the experiment (deactivation of facilities).
Publications
PRINCIPAL INVESTIGATOR(S)
OHTA Haruhiko [Kyushu University] / ASANO Hitoshi [Kobe University]
Unless specified otherwise, rights to all images belong to ©JAXA